Enhancing Your Welding WPS: Techniques for Improved Performance and Effectiveness
Enhancing Your Welding WPS: Techniques for Improved Performance and Effectiveness
Blog Article
Unlocking the Power of Welding WPS: Methods for Effectiveness and Safety And Security in Construction
In the world of construction, Welding Procedure Specifications (WPS) stand as the backbone of welding procedures, dictating the necessary steps for accomplishing both effectiveness and safety in the fabrication process. Recognizing the details of WPS is critical to using its complete potential, yet numerous companies battle to open truth power that exists within these files (welding WPS). By diving into the approaches that optimize welding WPS, a world of improved performance and enhanced safety waits for those ready to explore the subtleties of this vital aspect of manufacture

Significance of Welding WPS
The value of Welding Procedure Specs (WPS) in the fabrication sector can not be overemphasized. WPS act as a crucial roadmap that outlines the essential actions to make certain welds are performed constantly and correctly. By specifying important criteria such as welding processes, products, joint layouts, preheat temperature levels, interpass temperatures, filler steels, and post-weld warmth therapy demands, WPS supply a standardized technique to welding that improves performance, quality, and safety and security in construction processes.
Adherence to WPS aids in attaining harmony in weld top quality, decreasing the likelihood of defects or architectural failings. This standardization likewise facilitates compliance with industry regulations and codes, guaranteeing that produced frameworks satisfy the needed safety standards. In addition, WPS paperwork enables welders to reproduce effective welding procedures, leading to regular outcomes across various tasks.
Fundamentally, the precise development and rigorous adherence to Welding Treatment Specifications are extremely important for promoting the stability of welded frameworks, guarding versus possible threats, and promoting the online reputation of manufacture companies for supplying high-grade products and services.
Key Aspects of Welding WPS

Enhancing Effectiveness With WPS
When enhancing welding operations, leveraging the crucial components detailed in Welding Procedure Specs (WPS) comes to be vital for enhancing procedures and making best use of productivity. One means to boost efficiency with WPS is by meticulously choosing the ideal welding parameters.
Additionally, proper training and accreditation of welders in understanding and carrying out WPS can even more improve efficiency. Making sure that all team participants are fluent in analyzing and performing the WPS accurately can reduce mistakes and remodel, saving both time and sources. Regularly reviewing and my company upgrading the WPS to include any lessons learned or technical advancements can additionally add to performance improvements in welding procedures. By accepting the guidelines set forth in the WPS and continually seeking ways to enhance procedures, fabricators can accomplish greater efficiency degrees and remarkable end results.
Ensuring Safety And Security in Fabrication
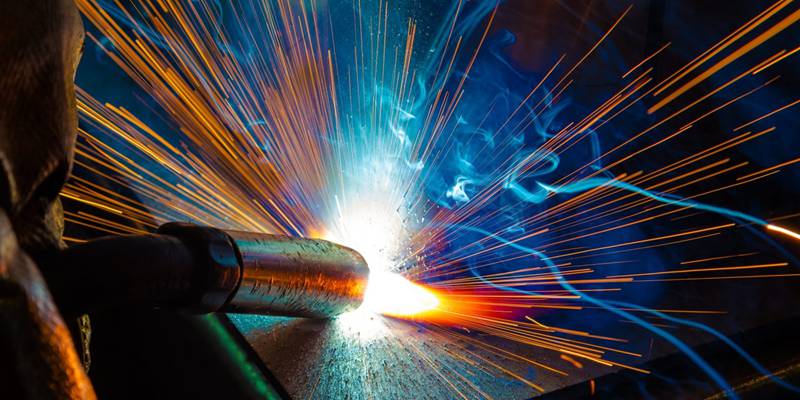
Safety and security methods in fabrication play a pivotal duty in guarding personnel and optimizing functional procedures. Guaranteeing security in fabrication involves a diverse technique that includes numerous elements of the welding procedure. One essential facet is the provision of individual protective tools (PPE) tailored to the specific hazards present in the fabrication environment. Welders need to be equipped with suitable gear such as safety helmets, handwear covers, and protective clothing to minimize risks associated with welding tasks.
Furthermore, adherence to appropriate air flow and fume extraction systems is essential in maintaining a healthy and balanced work environment. Welding fumes consist of damaging compounds that, if inhaled, can pose serious health threats. Executing effective air flow steps assists to reduce direct exposure to these dangerous fumes, advertising respiratory system wellness among employees.
Regular devices maintenance and assessments are additionally necessary for guaranteeing safety and security in fabrication. Damaged machinery can result in mishaps and injuries, underscoring the importance of prompt fixings and regular checks. By focusing on precaution and promoting a culture of awareness, manufacture facilities can develop a productive and secure workplace for their employees.
Executing WPS Finest Practices
To enhance functional efficiency official source and ensure top quality results in manufacture procedures, integrating Welding Procedure Specification (WPS) finest methods is vital - welding WPS. Implementing WPS finest methods entails precise preparation, adherence to industry requirements, and continuous monitoring to ensure optimal results. To start with, choosing the ideal welding procedure, filler material, and preheat temperature specified in the WPS is vital for accomplishing the preferred weld quality. Second of all, making sure that certified welders with the needed accreditations execute the welding procedures according to the WPS guidelines is necessary for uniformity and dependability. On a regular basis upgrading and reviewing WPS documents to mirror any kind of process improvements or changes in products is additionally a crucial finest practice to preserve precision and relevance. Furthermore, giving thorough training to welding workers on WPS requirements and best practices promotes a culture of safety and quality within the fabrication environment. By vigilantly executing WPS best methods, fabricators can simplify their procedures, decrease errors, and supply superior items to satisfy client assumptions.
Verdict
To conclude, welding WPS plays a critical role in making sure effectiveness and safety and security in manufacture processes. By concentrating on crucial elements, boosting efficiency, and executing best techniques, companies can maximize their welding operations. It is necessary to prioritize safety and security procedures to stop mishaps and make sure a smooth production process. By complying with these strategies, companies can unlock the complete capacity of welding WPS in their construction operations.
In the world of manufacture, Welding Treatment Specs (WPS) stand as the backbone of welding procedures, dictating the essential steps for accomplishing both effectiveness and safety in the manufacture procedure. By specifying necessary parameters such as welding processes, materials, joint styles, preheat temperatures, interpass temperatures, filler metals, and post-weld Continue warm treatment demands, WPS give a standardized strategy to welding that enhances efficiency, quality, and safety in fabrication procedures.

When maximizing welding operations, leveraging the vital elements outlined in Welding Treatment Specs (WPS) becomes vital for simplifying processes and maximizing performance. (welding WPS)
Report this page